Expert Packaging Machine Repair for Seamless Production Efficiency
Expert Packaging Machine Repair for Seamless Production Efficiency
Blog Article
The Ultimate Guide to Packaging Device Repair Work: Maintain Your Workflow Running Smoothly
Understanding the details of packaging equipment repair is vital for maintaining ideal efficiency and lessening disturbances. Regular maintenance not just expands the life of these makers however also addresses common problems that can hinder productivity.
Value of Normal Upkeep
Regular upkeep of packaging devices is vital for making sure optimal performance and longevity. By executing a structured maintenance routine, operators can determine possible issues before they rise into significant issues. This aggressive approach not just lessens downtime however additionally expands the life expectancy of the equipment, ultimately leading to reduced operational expenses.
Normal inspections enable the assessment of vital components such as belts, sensing units, and seals. Attending to wear and tear quickly protects against unforeseen failings that can disrupt production and cause costly repair work. In addition, routine upkeep assists make sure compliance with sector standards and laws, cultivating a risk-free workplace.
Furthermore, maintenance tasks such as lubrication, calibration, and cleansing significantly boost maker effectiveness. Boosted performance translates to regular item high quality, which is important for keeping client contentment and brand credibility. A properly maintained packaging equipment operates at optimum speeds and decreases material waste, adding to total efficiency.
Usual Packaging Device Concerns
Packaging equipments, like any complex equipment, can encounter a variety of typical concerns that might hinder their efficiency and effectiveness - packaging machine repair. One common trouble is irregular securing, which can cause product wasting and wastage if plans are not properly secured. This typically results from misaligned elements or worn securing aspects
One more regular concern is mechanical jams, which can happen as a result of international items, used parts, or improper placement. Jams can trigger delays in manufacturing and boost downtime, ultimately influencing general performance. Furthermore, electronic malfunctions, such as failure in sensors or control systems, can interfere with procedures and lead to incorrect dimensions or irregular equipment behavior.
Moreover, issues with item feed can additionally arise, where items might not be delivered to the packaging area regularly, causing disturbances. Wear and tear on rollers and belts can lead to suboptimal efficiency, requiring immediate focus to stop more damages.
Understanding these usual problems is crucial for keeping the stability of product packaging operations, making sure that equipment runs efficiently and efficiently, which in turn assists in conference manufacturing targets and maintaining product high quality.
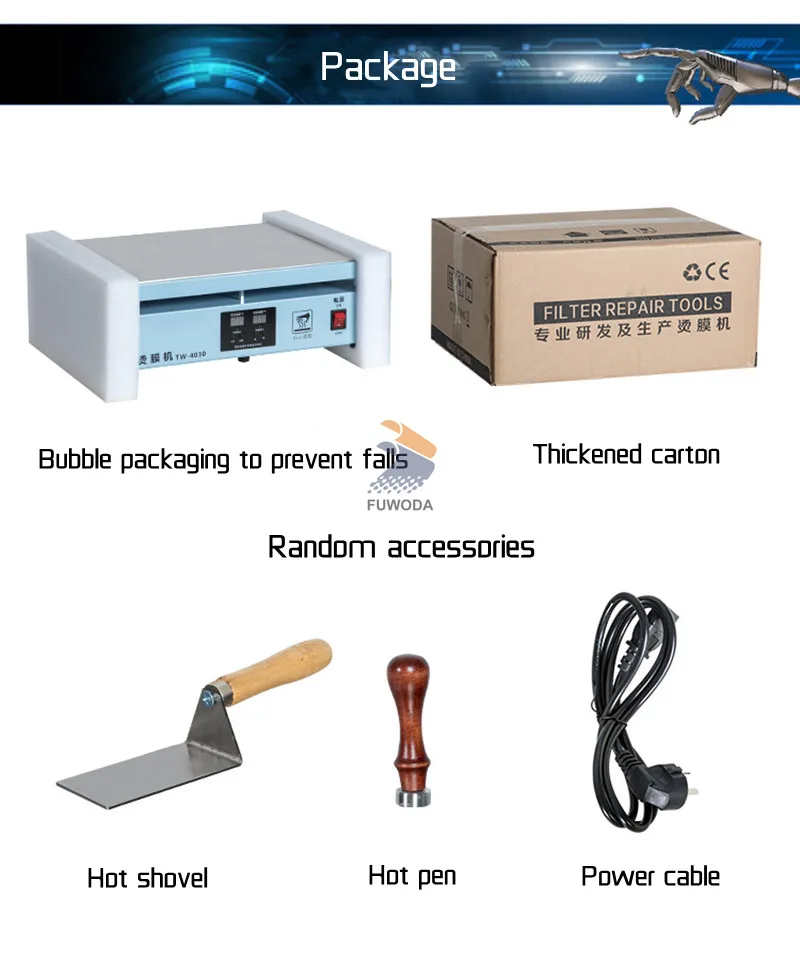
Troubleshooting Techniques
Effective repairing methods are vital for quickly addressing concerns that occur with product packaging makers. A methodical approach is crucial for determining the origin cause of breakdowns and reducing downtime. Begin by collecting info about the signs observed; this may consist of unusual noises, functional delays, or error codes shown on the machine's user interface.
Following, refer to the equipment's handbook for repairing guidelines certain to the model in concern. This resource can provide useful understandings into typical concerns and suggested analysis actions. Use aesthetic inspections to inspect for loosened connections, used belts, or misaligned parts, as these physical elements usually contribute to operational failings.
Apply a process of elimination by screening individual device functions. For instance, if a seal is not forming properly, examine the securing mechanism and temperature setups to establish if they meet operational specs. File each action taken and the results observed, as more helpful hints this can aid in future fixing efforts.
Repair service vs. Substitute Choices
When faced with equipment malfunctions, deciding whether to repair or replace a packaging maker can be a complicated and vital option. This decision pivots on numerous crucial aspects, consisting of the age of the equipment, the level of the damage, and the projected impact on functional effectiveness.
First of all, consider the machine's age. Older equipments might require more frequent repairs, bring about greater cumulative prices that can exceed the investment in a brand-new system. Additionally, review the intensity of the malfunction. Small issues can commonly be solved quickly and affordably, whereas considerable damage could require a significant economic commitment for fixings.
Functional downtime is another vital consideration. If fixing the machine will create prolonged delays, spending in a new maker that offers boosted efficiency and dependability could be more prudent. Additionally, think about the schedule of components; if replacement components are difficult to find by, it may be a lot more critical to replace the device completely.
Ultimately, carrying out a cost-benefit analysis that includes both instant and long-lasting ramifications will certainly help in making a notified decision that aligns with your operational goals and monetary restrictions. (packaging machine repair)
Safety Nets for Longevity
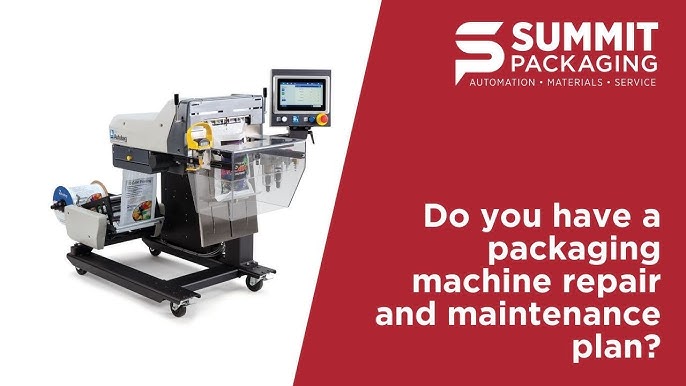
Trick safety nets include regular lubrication of relocating components, placement checks, and calibration of sensors and controls. Establishing a cleaning routine to eliminate particles and impurities from machinery can dramatically reduce wear and tear (packaging machine repair). Furthermore, keeping an eye on functional criteria such as temperature level and resonance can aid detect irregularities early on
Training staff to recognize indications of wear or malfunction is one more important element of precautionary maintenance. Equipping operators with the knowledge to perform basic troubleshooting can lead to quicker resolutions and minimize functional disturbances.
Documents of upkeep activities, including service records and Check Out Your URL inspection searchings for, cultivates responsibility and assists in notified decision-making concerning repairs and substitutes. By prioritizing safety nets, services can guarantee their packaging devices operate at peak efficiency, eventually leading to raised efficiency and decreased functional expenses.
Conclusion
To conclude, the efficient repair and maintenance of product packaging machines are paramount for maintaining operational performance. Routine maintenance alleviates the risk of usual problems, such as irregular sealing and mechanical jams, while organized troubleshooting methods promote timely resolution of breakdowns. Moreover, careful factor to consider of repair versus substitute choices adds to cost-effective administration of sources. By applying preventive measures, companies can boost machine durability and make certain continuous performance in product packaging operations.
Comprehending the ins and outs of product packaging see this website equipment repair service is crucial for maintaining optimal performance and reducing interruptions.Routine maintenance of packaging makers is vital for making certain optimum efficiency and long life.Product packaging equipments, like any kind of intricate equipment, can run into a selection of usual concerns that might impede their performance and efficiency. If repairing the machine will certainly create long term hold-ups, investing in a new machine that offers improved effectiveness and dependability might be more sensible.In verdict, the efficient maintenance and repair of product packaging equipments are vital for sustaining operational performance.
Report this page